Part of running a successful fashion brand is managing your resources well. That includes ordering the right amount of fabric you need without running short or sitting on a bunch of leftover yardage. Throughout development, your patternmaker and samplemaker will help you estimate and then finalize how much fabric you need to make your design. This is known as the style’s yield. The yield certainly is affected by the type of garment it is, but it is affected by many other things as well. Having a better understanding of what affects your yields will help you order materials more efficiently.
Yields are measured in linear yards (or fractions or decimals of a linear yard). Because yields are not measured as area, the fabric width really matters. One linear yard of a 60” wide fabric is a third more fabric area than one linear yard of a 45” wide fabric. More pattern pieces can be cut side by side along a wider fabric, thus decreasing the yield (linear distance) for the style.
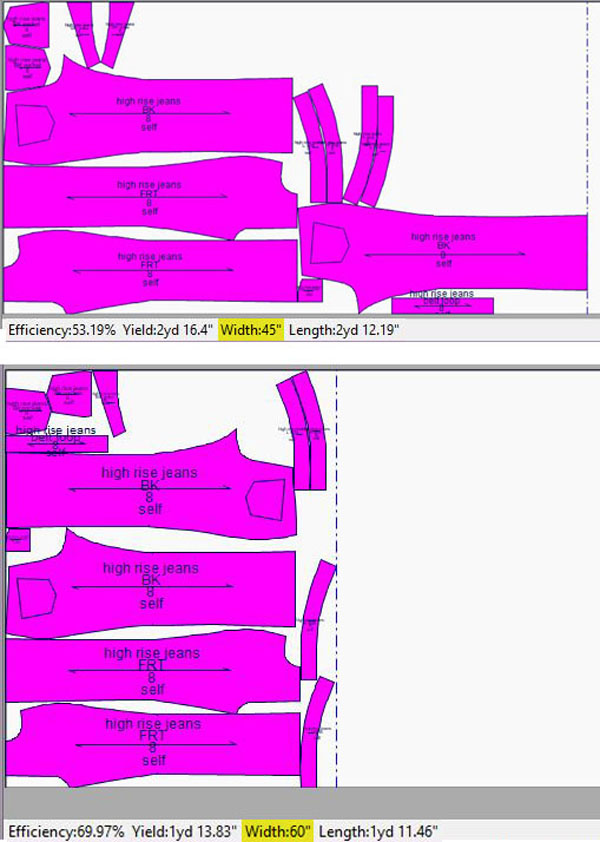
Another big factor in determining yield is the number of garments you are cutting at once. Cutting one garment can take a lot more fabric than cutting multiple. This is because when you cut multiple garments at once, you can nest the pieces together more efficiently. When cutting one, your yield is determined, in part, by the longest pattern piece. You may need more fabric to cut the long piece even if there is leftover width left unused. Cutting multiple garments would use up that extra fabric.
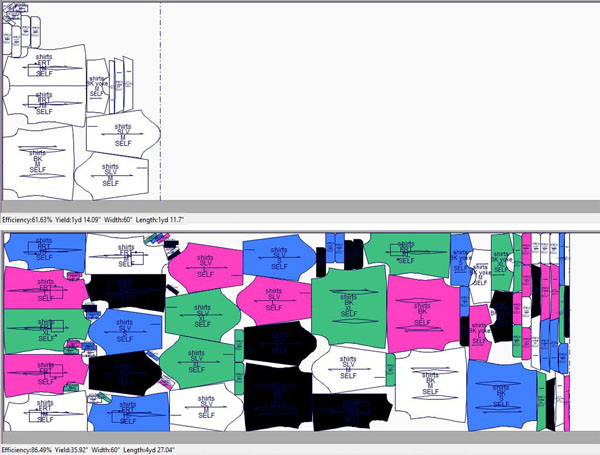
Even at a production scale, cutting more garments at a time will usually decrease your fabric yield. The longer the cutting table your factory has, the more efficient your yield will be. Several inches of fabric is wasted on the ends of each ply of fabric that is stacked on the cutting table. If your factory has a short table and has to stack many short plys, you will need more fabric than if they can cut fewer, longer plys. This difference is way less drastic than between cutting one and cutting multiple garments, but it can still make a difference on how much fabric you’ll need for your production run.
What size and size ratio you are cutting also influences how much fabric you’ll need. Yields should be calculated based on your middle size because theoretically the smaller sizes balance out the larger ones. Your middle size should also be your base size during development (meaning that pattern is done ahead of the other sizes) and can be used for yield estimates early on. If in production you end up cutting more larger sizes, you will need to order more fabric. If you cut each size separately instead of nesting them together, this can also use up more fabric as the larger sizes may not nest as nicely as the smaller ones.
The number of seam lines and pieces in your garment also has an effect on yields. Usually smaller pattern pieces take up less fabric collectively as they can fit in between the bigger pieces and use up all the scraps. Larger pattern pieces leave more wasted fabric between them.
A final thing to think about when calculating fabric yield is whether your design has any self-fabric bias trim, block fusing, or binding that will need to be cut separately. In sampling, these can often take up alot of fabric (again because of length needs). During production, there are often minimum yardage requirements to go through a bulk process of creating binding. Ask your factory about their requirements before deciding how much fabric to purchase for production.
Calculating the fabric usage of your design is not always as straightforward as looking at the type of garment. Your patternmaker, samplemaker, and factory will be able to help you determine your final fabric requirements, but it’s good to understand for yourself some of the factors play into that calculation.