This two-part blog post was originally published as a guest post on the KRSTN NDRSN blog. KRSTN NDRSN is a swimwear + intimates freelance design studio for purpose-driven fashion brands. The beautiful 3D renderings in these posts are done by Trudy Gardner on the KRSTN NDRSN team.
This post is part two of this series on how to draft patterns for stretch materials. Read part one on Planning Fit & Materials here.
Once you’ve selected your stretch materials and planned the fit of the garment, it is time to start drafting your pattern. The pattern harnesses the stretch properties of your fabric to shape the fit and hug and support the wearer in all the right places. It is at this stage that creative design gets technical.
Start from a pattern block
Drafting patterns for stretch fabrics isn’t easy, but certain shortcuts can make it much easier. One of my favorite shortcuts to drafting any pattern is to start with a tested pattern block. A pattern block is a similar style that you know fits and sells well. If you have one of these styles made for a similar fabric to the one you are drafting, you can use that pattern as a starting point. Using a tested pattern lets you know that the basic fit is good, and you just need to adjust the design details to match your new design.
It is crucial here to select a block pattern that is made for the same type of fabric as you are working with. Ideally, it might be the same exact fabric, but it is at least very close in weight and stretch properties. You wouldn’t want to use a stretch woven pattern as a block for a 4-way stretch knit style or vice versa. The goal is to build upon the fit you’ve already tested in this type of fabric.
Balance fabric stretch and contour seaming for the best fit
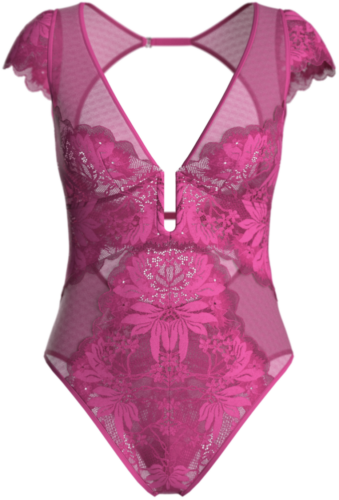
High-stretch materials can replace many darts and contour seams to create shaping. There are times, though, when you want to use a combination of fabric stretch and other contouring techniques to create the design, fit, and support you want. Areas that need to closely fit the body’s curves – like a bra cup – benefit from seams or darts. High-stretch materials can stretch around these curves but will squish and flatten the body tissue, adding more stress to the fabric.
Contour seams in the pattern not only make it easier to fit curves precisely, but they can also provide support. A seam or line of stitching through a stretch fabric will stabilize that area and prevent excess stretching. The stitching acts as reinforcement. For even more structure, you can add elastic to trim tape to the seam. This can be a great option for the areas in the garment that need extra support.
This is a functional and aesthetic conversation, so the designer and patternmaker will likely be involved in finding the right balance here. When discussing fabric stretch versus contour seaming, keep in mind how your design will fit on different body sizes and shapes. You might be able to rely on the fabric stretch alone in smaller or flat-chested sizes, but not in larger or fuller-bust sizes. You want to design and pattern with your whole size range in mind.
Don’t forget about shrinkage
When drafting for stretch materials, it is obvious to consider the stretch, but don’t forget to consider shrinkage as well. As with any fabric, you’ll want to test your stretch fabrics under normal care and wear conditions to anticipate any shrinkage. I recommend doing this right after you’ve selected your materials. You’ve dialed in your pattern to get the right fit so far, so it would be a shame to have that precision thrown off by the final garment shrinking in the first wash. (I had a bra once that came out of the wash with the shell fabric so shrunken that it was pulling the top edge of the bra cup outward in a way that was immediately noticeable through any shirt – super annoying.)
Beyond just washing shrinkage, stretch fabrics for swimwear and intimates are also exposed to chlorine, salt water, sunlight, sweat, etc. which can change the fabric properties and require adjustments to the pattern to compensate. Stretch fabrics can shrink depending on how they were unrolled and laid out to cut or if they come in contact with heat from printing or ironing during production. You can draft your pattern to counteract all these types of shrinkage if you’ve tested your fabric and have the information needed.
Include trim cut length guides
Some stretch fabric garments like tee shirts require minimal trims. Swimwear and intimate designs, on the other hand, often include multiple components like elastics, ribbons, stabilizers, hardware closures, rings, sliders, etc. Any of these that require cutting (i.e. not in piece units like a slider) should have a cut length guide in the pattern. These are not pattern pieces that will be cut in a marker from the fabric, but they are guides that make it easy to measure and cut how much of each trim is needed for each size.
It is especially important to include cut length guides for trims that will finish at a different length than the length of the pattern seam line. For example, when adding elastic to the leg openings of a panty, the elastic might be pulled during sewing to slightly ease the fabric into the seam. This means that the elastic length is shorter than the length of the leg opening on the pattern. You’ll need to specify the exact elastic length in the pattern cut guide to ensure every garment gets sewn the same way.
Stretch materials are wonderfully flexible and lend so many properties to the fit of the finished garment. They can be tricky to draft patterns for, though, if you’re not used to managing them. Follow these pattern drafting tips and techniques to get that perfect fit for your next swimwear or intimate apparel garment.